Chemical engineers have generated ultra-pure green light for the first time.
The new light-emitting diode paves the way for visibly improved color quality in a new generation of ultra-high definition displays for TVs and smartphones.
Electronic devices must first be able to produce ultra-pure red, blue, and green light in order to enable the next generation of displays to show images that are clearer, sharper, richer in detail, and with a more refined range of colors. For the most part, this is already possible for red and blue light; green light, however, has been at the limits of technology.
This is due mainly to human perception, since the eye is able to distinguish between more intermediary green hues than red or blue ones. “This makes the technical production of ultra-pure green very complex, which creates challenges for us when it comes to developing technology and materials,” says Sudhir Kumar of ETH Zurich, co-lead author of the study.
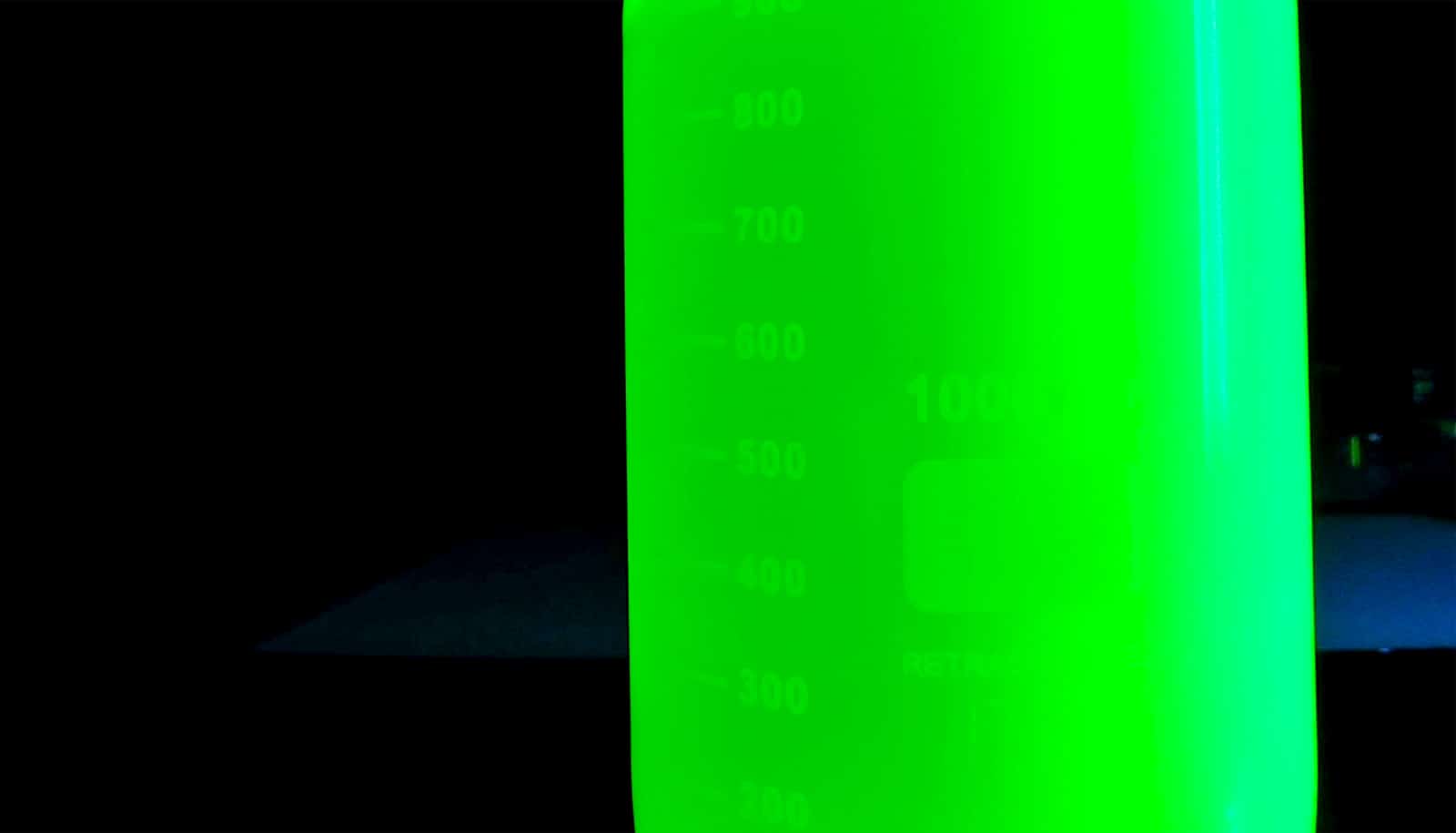
Ultra-pure green plays a key role in extending the color range, or gamut. Ultimately, new hues arise from the technical mixture of three base colors: red, blue, and green. The purer the base colors, the broader the range of hues a screen can display. The new LED is in line with 97 to 99 percent of the international standard for Ultra HD, Rec.2020. By comparison, the purest color TV displays currently available on the market cover on average only 73.11 to 77.72 percent; none exceeds 80 percent.
How they did it
Chih-Jen Shih, professor of chemical engineering, and colleagues have effectively developed an ultra-thin, bendable light-emitting diode able to emit pure green light using simple room-temperature processes. Shih says that this is the second aspect of his breakthrough and is at least equally important, as until now high-temperature processes were required to produce pure light with LED technology.
“Because we were able to realize the entire process at room temperature, we’ve opened up opportunities for the simple, low-cost industrial production of ultra-green light-emitting diodes in the future,” says Jakub Jagielski, co-lead author of the report.
More specifically, Shih and his team used nanomaterials to further develop the LED technology. A light-emitting diode usually contains a semiconductor crystal that converts electrical current passed through it into radiant light. The raw material is usually indium gallium nitride (InGaN); however, this material does not have the ideal properties for production of ultra-pure green light. So Shih’s team instead used perovskite, a material that is also used in the manufacture of solar cells and which can convert electricity into light relatively efficiently. It is also inexpensive and helps make the manufacturing process simple and fast—it takes just half an hour to chemically clean perovskite and make it ready for use, says Shih.
The perovskite material in Shih’s light-emitting diode is a miniscule 4.8 nanometers in thickness. This is an important factor, since the color quality depends on the thickness and form of the nanocrystal used.
In order to reach the desired pure green, the crystals should not be any thicker or thinner. These flexible, ultra-thin light-emitting diodes are as bendable as a sheet of paper. Hence, they can be produced inexpensively and quickly using the existing roll-to-roll process for example. Shih says this will also benefit industrial production in the future.
Next steps
However, it will still take some time before we see the first industrial application of ultra-green light-emitting diodes. The next step for Shih is to first improve the efficiency. Today, his LED works at 3 percent efficiency when converting electricity into light; in comparison, TV screens currently available on the market have efficiency values of 5 to 10 percent. Shih is hoping that the next version will be 6 to 7 percent more efficient.
He also sees potential for improvement in the lifespan of his light-emitting diode. Currently, it illuminates for about two hours, whereas screens available on the market should work for many years.
Wendelin Stark, professor of functional materials engineering at ETH Zurich, along with researchers from South Korea and Taiwan, also contributed to work, which appears in Nano Letters.
Source: Florian Meyer for ETH Zurich