The “Flash Joule” technique could be a profitable way to turn plastic waste into nanomaterials, report researchers.
The amount of plastic waste produced globally has doubled over the past two decades—and plastic production is expected to triple by 2050—with most of it ending up in landfills, incinerated, or otherwise mismanaged, according to the Organization for Economic Cooperation and Development. Some estimates suggest only 5% is actually being recycled.
“Waste plastic is rarely recycled because it costs a lot of money to do all the washing, sorting, and melting down of the plastics to turn it into a material that can be used by a factory,” says Kevin Wyss, a Rice University graduate student and lead author of a study in the journal Advanced Materials. The paper describes how he and colleagues in the lab of chemist James Tour used their flash Joule heating technique to turn plastic into valuable carbon nanotubes and hybrid nanomaterials.
“We were able to make a hybrid carbon nanomaterial that outperformed both graphene and commercially available carbon nanotubes,” Wyss says.
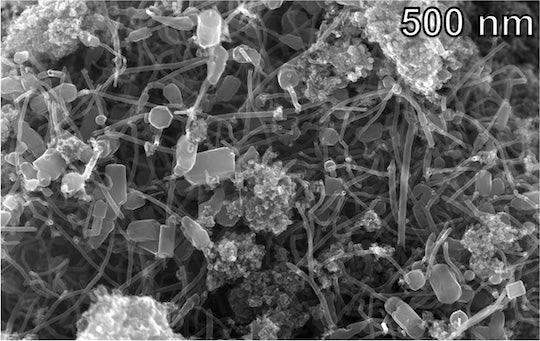
Nanomaterial ‘sprouts’
Graphene, carbon nanotubes, and other carbon-based nanomaterials are generally strong and chemically robust, have low density and lots of surface area, and possess conductivity and broadband electromagnetic absorption abilities. This makes them useful in a variety of industrial, medical, and electronics applications such as composites, coatings, sensors, electrochemical energy storage, and more.
“What was really interesting about our results this time is that we were able to make these carbon nanotubes with bits of graphene attached on the ends,” Wyss says. “You can think of the structure of this new hybrid nanomaterial as similar to bean sprouts or lollipops. These are normally really hard to make, and the fact that we were able to make them out of waste plastic is really special.”
The structure of the new hybrid carbon nanomaterial is responsible for its enhanced performance.
“Let’s say I was trying to pull a string of yarn out of a sweater,” Wyss says. “If the string is straight and smooth, it can come out quite easily sometimes and ruin the weave. It’s the same with the carbon nanotubes; having these masses of graphene attached at the ends helps make them much harder to remove, thereby strengthening the composite.
“You can also think of it this way: If you get a splinter, it’s easy to take out. But if you get pricked with something that has a curve on the end, like a fishing hook, it’s a lot harder to take out,” he adds.
‘Flash’ the plastic waste
The plastic, which does not need to be sorted or washed as in traditional recycling, is “flashed” at temperatures over 3,100 kelvins (about 5,120 degrees Fahrenheit). “All we do is grind the material into small, confetti-sized pieces, add a bit of iron, and mix in a small amount of a different carbon—say, charcoal—for conductivity,” Wyss says.
“Recycling plastic costs more than just producing new plastic,” he adds. “There’s very little economic incentive to recycle plastic. That’s why we turned to upcycling, or turning low-value waste materials into something with a higher monetary or use value. If we can turn waste plastic into something more valuable, then people can make money off of being responsible in how they deal with discarded plastics.”
A life cycle analysis of the production process revealed that flash Joule heating was considerably more energy-efficient and environmentally friendly than existing nanotube production processes.
“Compared to commercial methods for carbon nanotube production that are being used right now, ours uses about 90% less energy and generates 90%-94% less carbon dioxide,” Wyss says.
The National Science Foundation Graduate Research Fellowship, the Air Force Office of Scientific Research, and the US Army Engineer Research and Development Center supported the research.
Source: Rice University