Flexible, lightweight, 4D-printed materials could lead to better shock absorbers, morphing airplane or drone wings, soft robotics, and tiny implantable biomedical devices, report researchers.
3D printing, also known as additive manufacturing, turns digital blueprints to physical objects by building them layer by layer. 4D printing is similar to this technology, but with one big difference: it uses special materials and sophisticated designs to print objects that change shape with environmental conditions such as temperature acting as a trigger, says senior author Howon Lee, an assistant professor in the mechanical and aerospace engineering department at Rutgers University. Time is the fourth dimension that allows them to morph into a new shape.
“We believe this unprecedented interplay of materials science, mechanics, and 3D printing will create a new pathway to a wide range of exciting applications that will improve technology, health, safety, and quality of life,” Lee says.
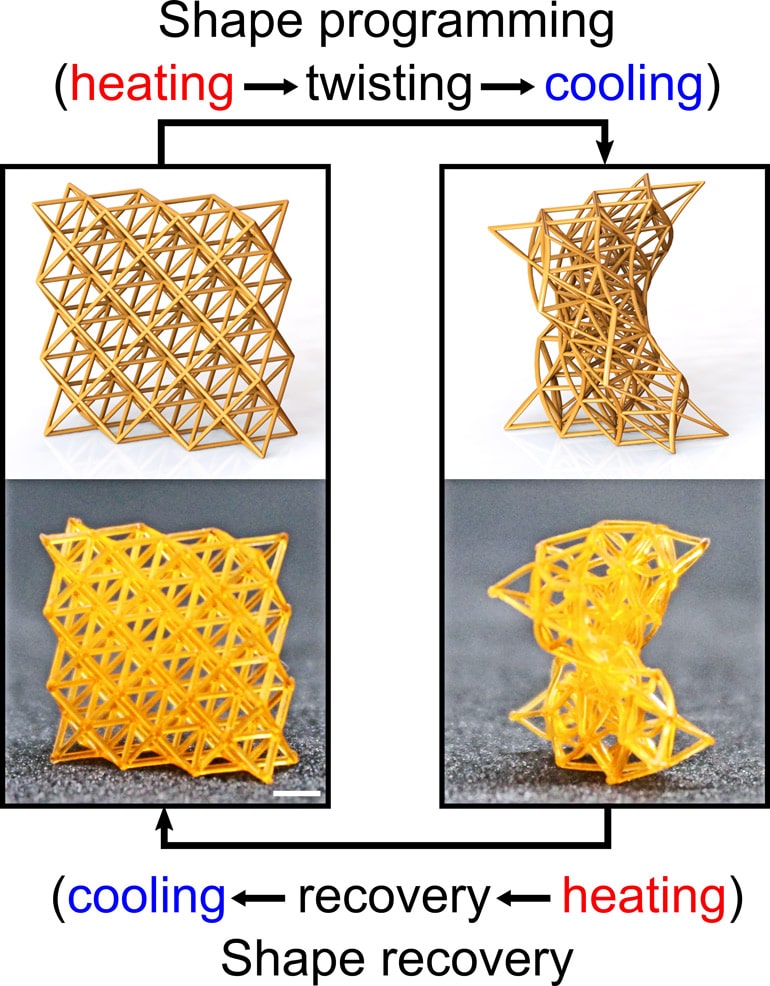
The engineers created a new class of “metamaterials”—materials engineered to have unusual and counterintuitive properties. The word metamaterials is derived from the Greek word “meta,” which means “higher” or “beyond.”
Previously, it wasn’t possible to reverse the shape and properties of metamaterials after manufacturing. But the researchers can tune their plastic-like materials with heat, so they stay rigid when struck or become soft as a sponge to absorb shock.
The researchers can adjust the stiffness more than 100-fold in temperatures between room temperature (73 degrees) and 194 degrees Fahrenheit, allowing great control of shock absorption. They can also reshape the materials for a wide variety of purposes. The materials can temporarily transform into any deformed shape and then return to their original shape on demand when researchers expose them to heat.
The materials could be useful in airplane or drone wings that change shape to improve performance, and in lightweight structures that collapse for space launches and reform in space for a larger structure, such as a solar panel.
Soft robots made of soft, flexible, and rubbery materials inspired by the octopus could have variable flexibility or stiffness that adapt to the environment and task at hand. Tiny medical devices doctors insert or implant in people for diagnosis or treatment could temporarily become soft and flexible for minimally invasive and less painful insertion into the body, Lee says.
Their research appears in the journal Materials Horizons. Additional coauthors are from Rutgers and the Korea University.
Source: Rutgers University