Some layered structures in nature—such as nacre, deer antlers, and conch shells—are super tough, but it’s not universal, warn researchers.
Nacre—the iridescent part of mollusk shells—is a poster child for biologically inspired design. Despite being made of brittle chalk, the intricately layered microstructure of nacre gives it a remarkable ability to resist the spread of cracks, a material property known as toughness.
Engineers looking to design tougher materials have long sought to mimic this kind of natural layering, but the new finding suggests a need for caution.
For the study in Nature Communications, researchers tested another layered microstructure renowned for its physical properties—the anchor spicules of a sea sponge called Euplectella aspergillum. The spicules are tiny filaments of layered glass that hold the sponges to the sea floor. The layered structure of the spicules is often compared to that of nacre, the researchers say, and it’s been assumed that the spicule structure similarly enhances toughness. This new study finds otherwise.
“Despite the similarities between the architectures of nacre and Euplectella spicules, we found that the spicule’s architecture does relatively little in terms of enhancing its toughness, contrary to a long-held assumption,” says study coauthor Max Monn, a recently graduated PhD student at Brown University.
Bending spicules until they snap
For the study, the researchers compared the toughness of Euplectella spicules to those of another sponge species, Tethya aurantia. Tethya spicules have a similar chemical composition to Euplectella spicules but lack the layered structure. To test toughness, the team put tiny notches in the spicules and then bent them. By measuring the energy consumed when cracks propagated from the notches under bending strain, the researchers could quantify the toughness of both types of spicules.
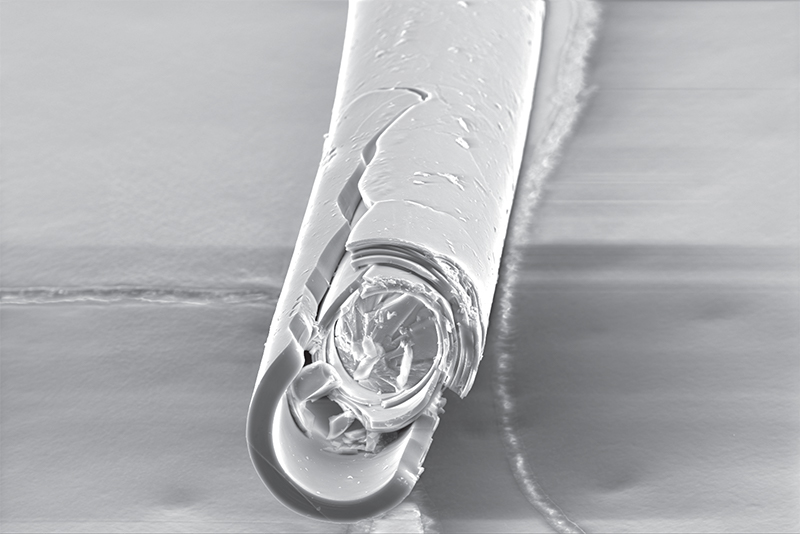
The experiments showed very little difference in toughness between the two spicules, which suggests that Euplectella‘s layering doesn’t provide much of a toughness enhancement.
Using computer modeling, the researchers were able to look deeper into why layering enhances toughness in some materials and not others. The models showed that the curvature of the layering in cylindrical spicules seems to turn off the toughness enhancement of layered structures. Flat layers, like those found in nacre, seem to prevent cracks from spreading from one layer to the next, the researchers say. But in materials with curved layers like the Euplectella spicules, cracks are able to jump from layer to layer rather than stopping between the layers.
Curvature and toughness
The findings reveal a previously unknown relationship between curvature and toughness in layered materials and have implications for the design of bio-inspired composite materials, says Haneesh Kesari, an assistant professor in Brown’s School of Engineering and the paper’s senior author.
“Specifically, it shows that if you adopt a layered architecture in order to enhance the toughness of a material, you should be careful of areas that require the layers to be curved,” Kesari says. “Our measurements of the spicules and results from our computational model show that curved layers don’t provide the same magnitude of toughness enhancements as when layers are flat.”
The findings don’t mean that the layered structure of Euplectella spicules isn’t interesting. Previous work from Kesari’s lab has shown that the layered structure seems to vastly increase the spicules’ bending strength—to withstand large bending curvatures before failing. But bending strength and toughness are very different mechanical properties, and helping to dispel the idea that layering always enhances toughness is a useful insight for bio-inspired design in general, the researchers say.
“Our study indicates that not all layered architectures provide significant toughness enhancement,” says Sayaka Kochiyama, a Brown graduate student and study coauthor. “That better understanding of structure-property relationship is necessary to avoid naive biomimicry.”
Support for the research came from the Office of Naval Research, the National Science Foundation, the American Society of Mechanical Engineers, and the NASA Rhode Island Space Grant Consortium.
Source: Brown University