Researchers have developed an inexpensive and scalable technique that can change plastic’s molecular structure to help it cast off heat.
Advanced plastics could usher in lighter, cheaper, more energy-efficient product components, including those used in vehicles, LEDs, and computers—if only they were better at dissipating heat.
The concept can likely be adapted to a variety of other plastics. In preliminary tests, it made a polymer about as thermally conductive as glass—still far less so than metals or ceramics, but six times better at dissipating heat than the same polymer without the treatment.
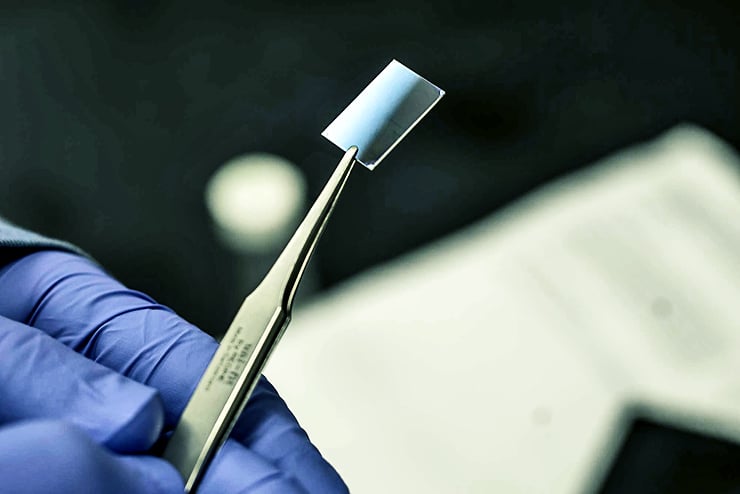
“Plastics are replacing metals and ceramics in many places, but they’re such poor heat conductors that nobody even considers them for applications that require heat to be dissipated efficiently,” says Jinsang Kim, a materials science and engineering professor at the University of Michigan. “We’re working to change that by applying thermal engineering to plastics in a way that hasn’t been done before.”
The process is a major departure from previous approaches, which have focused on adding metallic or ceramic fillers to plastics. This has met with limited success; a large amount of fillers must be added, which is expensive and can change the properties of the plastic in undesirable ways. Instead, the new technique uses a process that engineers the structure of the material itself.
Plastics are made of long chains of molecules that are tightly coiled and tangled like a bowl of spaghetti. As heat travels through the material, it must travel along and between these chains—an arduous, roundabout journey that impedes its progress.
The team used a chemical process to expand and straighten these molecule chains. This gave heat energy a more direct route through the material.
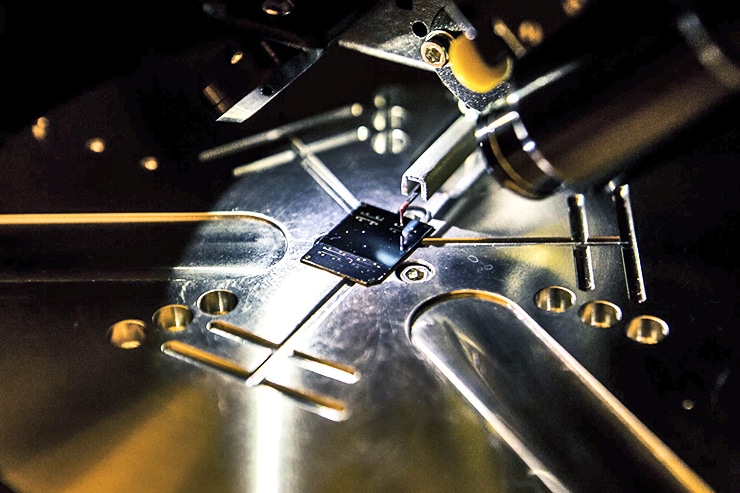
To accomplish this, the researchers started with a typical polymer, or plastic. They first dissolved the polymer in water, then added electrolytes to the solution to raise its pH, making it alkaline.
The individual links in the polymer chain—called monomers—take on a negative charge, which causes them to repel each other. As they spread apart, they unfurl the chain’s tight coils. Finally, the water and polymer solution is sprayed onto plates using a common industrial process called spin casting, which reconstitutes it into a solid plastic film.
The uncoiled molecule chains within the plastic make it easier for heat to travel through it. The team also found that the process has a secondary benefit—it stiffens the polymer chains and helps them pack together more tightly, making them even more thermally conductive.
How much plastic have humans made?
“Polymer molecules conduct heat by vibrating, and a stiffer molecule chain can vibrate more easily,” says Apoorv Shanker, a materials science and engineering graduate student. “Think of a tightly stretched guitar string compared to a loosely coiled piece of twine. The guitar string will vibrate when plucked, the twine won’t. Polymer molecule chains behave in a similar way.”
The researchers say that the work can have important consequences because of the large number of polymer applications in which temperature is important.
“Researchers have long studied ways to modify the molecular structure of polymers to engineer their mechanical, optical, or electronic properties, but very few studies have examined molecular design approaches to engineer their thermal properties,” says Kevin Pipe, an associate professor of mechanical engineering.
“While heat flow in materials is often a complex process, even small improvements in the thermal conductivities of polymers can have a large technological impact,” he says.
The team is now looking at making composites that combine the new technique with several other heat dissipating strategies to further increase thermal conductivity. They’re also working to apply the concept to other types of polymers beyond those used in this research. A commercial product is likely several years away.
How to make plastic from CO2 and plants
“We’re looking at using organic solvents to apply this technique to non- water soluble polymers,” says Chen Li, a mechanical engineering graduate researcher. “But we believe that the concept of using electrolytes to thermally engineer polymers is a versatile idea that will apply across many other materials.”
A paper outlining the findings appears in Science Advances.
Source: University of Michigan