A new eco-friendly technique converts aluminum and magnesium waste into high-value, multi-functional aerogels.
The upcycling method could be applied to all types of metal waste in powder form, such as metal chips and electronic waste, according to a new study.
With the growing demand for metal products, it is crucial to promote sustainable and environmentally-friendly methods of recycling metal waste to help reduce the environmental impact of using metals in the economy.
The conventional approaches for recycling metal waste are energy intensive and some of these methods also generate environmentally harmful byproducts, such as ammonia and methane during aluminum recycling.
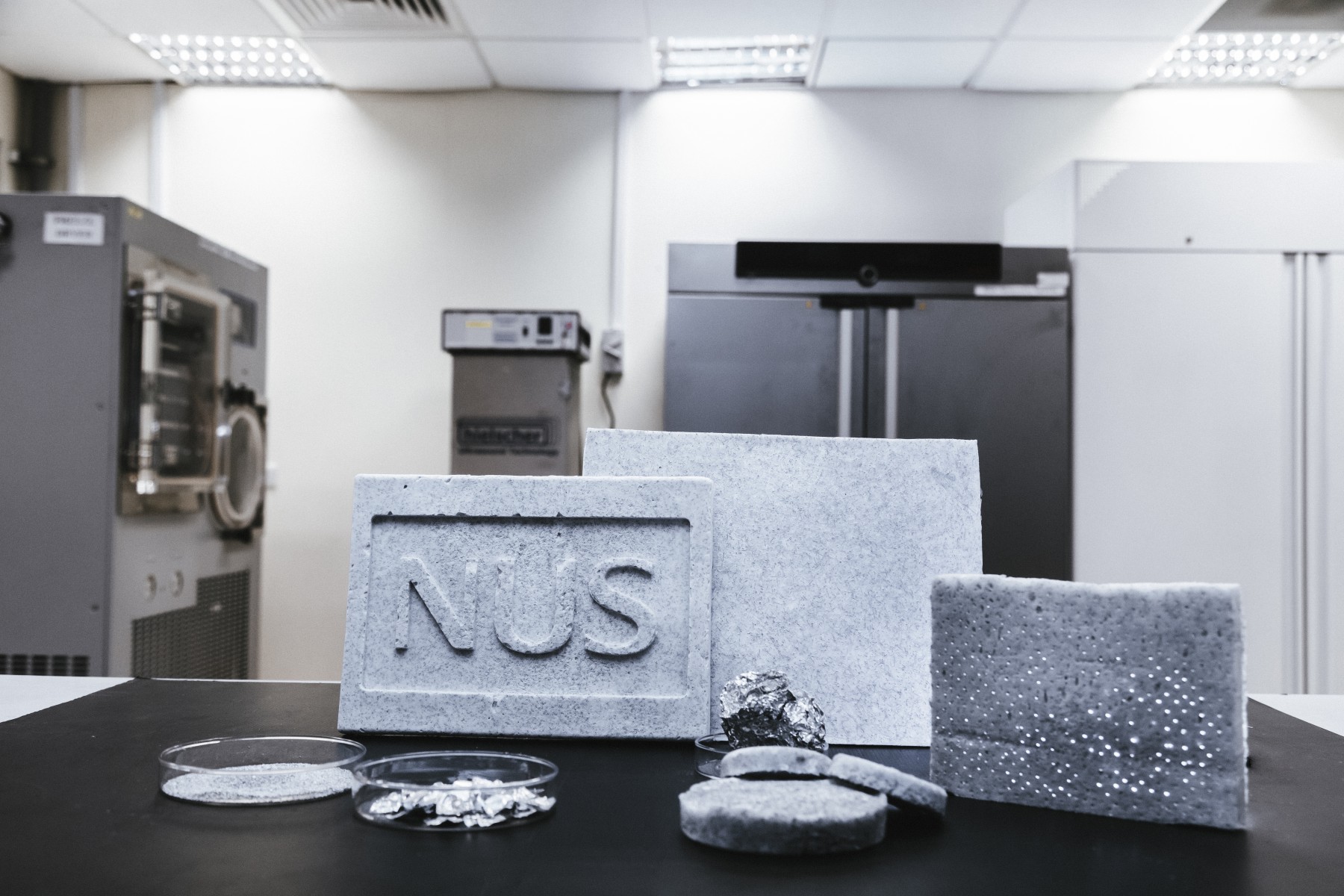
“Our approach is cheaper, does not produce any hazardous waste, consumes less energy, and is more environmentally-friendly than conventional recycling methods for metal waste,” says Duong Hai-Minh, associate professor in the mechanical engineering department at the National University of Singapore.
“The metal-based aerogels created using our unique fabrication technique have high thermal and mechanical stability. Hence, they are promising candidates for heat and sound insulation in harsh environments with high temperature or high mechanical impact. We are also exploring new uses for such aerogels, such as biomedical applications.”
Aerogels from waste
The latest technological breakthrough builds on the researchers’ earlier successes in developing aerogels using different types of waste such as plastics, textiles, paper, pineapple leaves, and other types of food and agricultural waste.
The team has developed a simple fabrication process to create metal-based aerogels. Metal waste is first ground into powder and mixed with chemical crosslinkers. The mixture is heated in the oven, frozen, and then freeze-dried to create the aerogel. The process may vary slightly depending on the metal waste involved. On average, it takes about one to three days to transform powdered metal waste into aerogels, compared to three to seven days using conventional methods of producing aerogels.
The simple process also means that metal-based aerogels can be produced at a much lower cost. Using the new technique, a piece of metal-based aerogel that is 1 square meter and 1 centimeter thick costs less than S$10.50 ($7.89 American dollars) to produce, half the price of commercially available silica aerogel.
Aerogels are highly absorbent, extremely light, and have excellent thermal and sound insulation capabilities. In earlier work, Duong and his team showed that the properties of aerogels can be altered by coating them with chemicals—for instance, they can become water repellent or fire resistant.
Translucent concrete
In their latest work, the researchers identified new exciting applications for metal-based aerogels, such as light-weight construction materials.
“Our aluminum aerogel is 30 times lighter and insulates heat 21 times better than conventional concrete. When optical fibers are added during the mixing stage, we can create translucent aluminum aerogels which, as building materials, can improve natural lighting, reduce energy consumption for lighting, and illuminate dark or windowless areas.
“Translucent concrete can also be used to construct sidewalks and speed bumps that light up at night to improve safety for pedestrians and road traffic,” Duong says.
The translucent aluminum aerogels are six times lighter, six times better in thermal insulation, and 120 times cheaper compared to commercial translucent concrete (LiTraCon).
When coated with a chemical called methyltriethoxysilane (MTEOS), aluminum aerogels can repel water and becomes a self-cleaning construction material which allows dirt or debris to be easily washed away when it comes in contact with water.
Metal-based aerogels are also suitable as fire retardant boards, thermal insulation materials in buildings, and piping systems for absorption of airborne contaminants for indoor environments and oil-spill cleaning.
Medical applications
The researchers are also looking at using aerogels for biomedical applications.
“We are currently working with a commercial partner to test our aluminum aerogels as microcarriers for cell cultivation. Microcarriers are micro-size beads for cells to anchor and grow. Our first trials were performed on stem cells, using a cell line commonly used for testing of drugs as well as cosmetics, and the results are very encouraging,” Duong says.
To be used as microcarriers, researchers grind aluminum aerogels into powder and add them to the mixture of cells and growth media (including nutrients, antibiotics, and growth supplements). They then cultivate the cells at 37 degrees Celsius (98.6 degrees Fahrenheit) in an incubator for 12 days. The researchers then remove the microcarriers and harvest the cells for various uses.
“After 12 days of incubation, our experiments obtained a yield of 70%. This is the first successful demonstration of growing cells using aerogels. We need to conduct more studies to optimize the culture conditions and address biocompatibility requirements. This is an exciting development that could open doors to a wider use of aerogels for non-conventional applications such as testing drugs and cosmetics, vaccine development, and tissue engineering,” Duong explains.
The team is in discussion with industry partners to commercialize the technology for fabricating metal-based aerogels. In the next phase of their research, the team is also looking at developing metal-based aerogels for applications that require extremely high temperature tolerance, such as for military applications.
The paper appears in the Journal of Material Cycles and Waste Management.
Source: National University of Singapore