Researchers have created a “map” to help in designing materials based on some of the toughest substances in nature.
How a material breaks could be the most important property to consider when designing layered composites that mimic those found in nature. The new map decodes the interactions between materials and the structures they form and can help maximize their strength, toughness, stiffness, and fracture strain.
In a study that required more than 400 computer simulations of platelet-matrix composite materials like mother-of-pearl, Rouzbeh Shahsavari, an assistant professor of civil and environmental engineering and of materials science and nanoengineering at Rice University, and visiting scholar Shafee Farzanian developed their design map to help with the synthesis of staggered composites for applications at any scale, from microelectronics to cars to spacecraft, where lightweight, multifunctional structural composites are key.
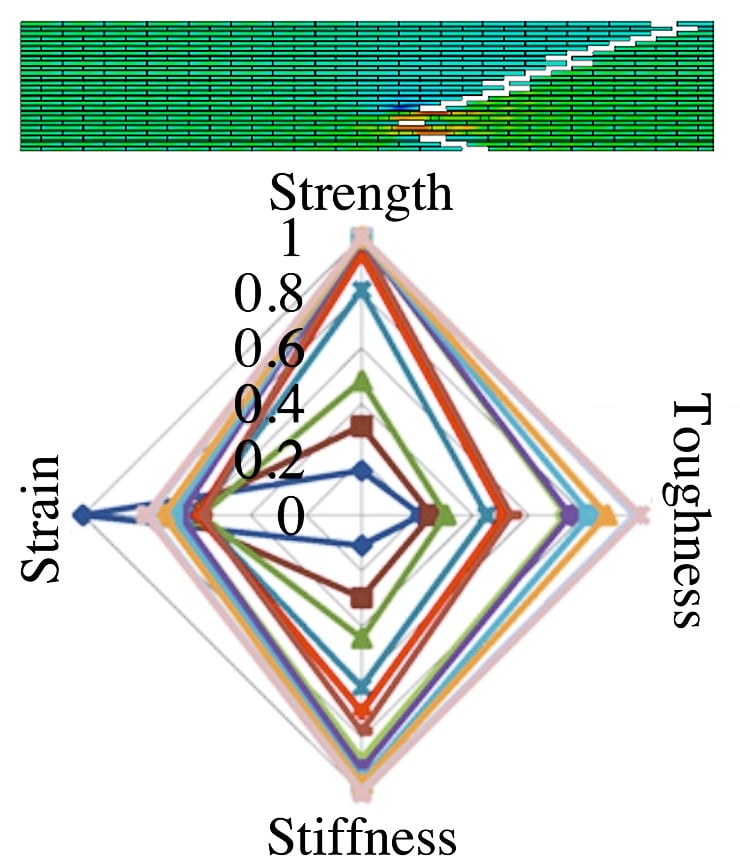
The model integrates the geometries and properties of various platelet and matrix components to compute the composite’s strength, toughness, stiffness and fracture strain. Changing any architectural or compositional parameter adjusts the entire model as the user seeks the optimal psi, a quantification of its ability to avoid catastrophic failure.
Holding up under pressure
Natural composites are common. Examples include nacre (mother-of-pearl), tooth enamel, bamboo, and the dactyl clubs of mantis shrimp, all of which are nanoscale arrangements of hard platelets connected by soft matrix materials and arranged in overlapping brick-and-mortar, bouligand, or other architectures.
They work because the hard parts are strong enough to take a beating and flexible enough (due to the soft matrix) to distribute stress throughout the material. When they fracture, they’re often able to distribute or limit the damage without failing entirely.
“Lightweight natural materials are abundant,” Shahsavari says. “In these types of materials, two kinds of toughening happen. One comes before crack propagation, when the platelets slide against each other to relieve stress. The other is part of the beauty of these materials: the way they toughen after crack propagation.
Tougher composite for teeth mimics sticky mussels
“Even when there is a crack, it does not mean a failure,” he says. “The crack may be arrested or deflected several times between the layers. Instead of going straight through the material to the surface, which is a catastrophic failure, the crack bumps into another layer and zigzags or forms another complex pattern that delays or entirely prevents the failure. This is because a long and complex crack trajectory requires much more energy to drive it, compared with a straight crack.”
Scientists and engineers have worked for years to replicate the light, tough, strong, and stiff properties of natural materials, either with hard and soft components or combinations of different platelet types.
Different characteristics
To engineers, stiffness, toughness, and strength are distinct characteristics. Strength is the ability of a material to stay together when stretched or compressed. Stiffness is how well a material resists deformation. Toughness is the ability of a material to absorb energy before failure. In a previous paper, the Rice lab created maps to predict the properties of composites based on those parameters before crack propagation.
The addition of crack-induced toughening in natural and biomimetic materials, Shahsavari says, is another potent and interesting source of toughening that provides extra lines of defense against failure.
“The models uncovered non-intuitive synergies between the before- and after-crack toughening phenomena,” he says. “They showed us what architectures and components would allow us to combine the best properties of each.”
The baseline model allowed the researchers to adjust four values for each simulation: characteristic platelet length, plasticity of the matrix, the platelet dissimilarity ratio (when more than one type of platelet is involved), and the platelet overlap offset, all of which are important to the composite’s properties.
Over the course of the simulations, the model revealed the greatest factor in psi may be platelet length, Shahsavari says. It showed that short platelets largely yield fracture control to the plasticity of the soft matrix, while long platelets take it back. Platelet lengths that distribute the fracture evenly and allow maximum crack growth can achieve the optimal psi and make material better able to avoid catastrophic failure.
Mussel shells aren’t as thick as they used to be
The model will also help researchers design whether a material will fail with a sudden fracture, like ceramics, or slowly, like ductile metals, by switching components, using contrasting platelets, or changing the architecture.
The National Science Foundation and Rice’s Department of Civil and Environmental Engineering supported the research. Tthe National Institutes of Health and an IBM Shared University Research Award in partnership with Cisco, Qlogic, and Adaptive Computing, as well as Rice’s National Science Foundation-supported DAVinCI supercomputer administered by the Center for Research Computing and procured in partnership with Rice’s Ken Kennedy Institute for Information Technology provided supercomputing resources.
Source: Rice University