An advanced space engine in the running to propel humans to Mars has broken records for operating current, power, and thrust for a device of its kind, known as a Hall thruster.
Hall thrusters offer exceptionally efficient plasma-based spacecraft propulsion by accelerating small amounts of propellant very quickly using electric and magnetic fields. They can achieve top speeds with a tiny fraction of the fuel required in a chemical rocket.
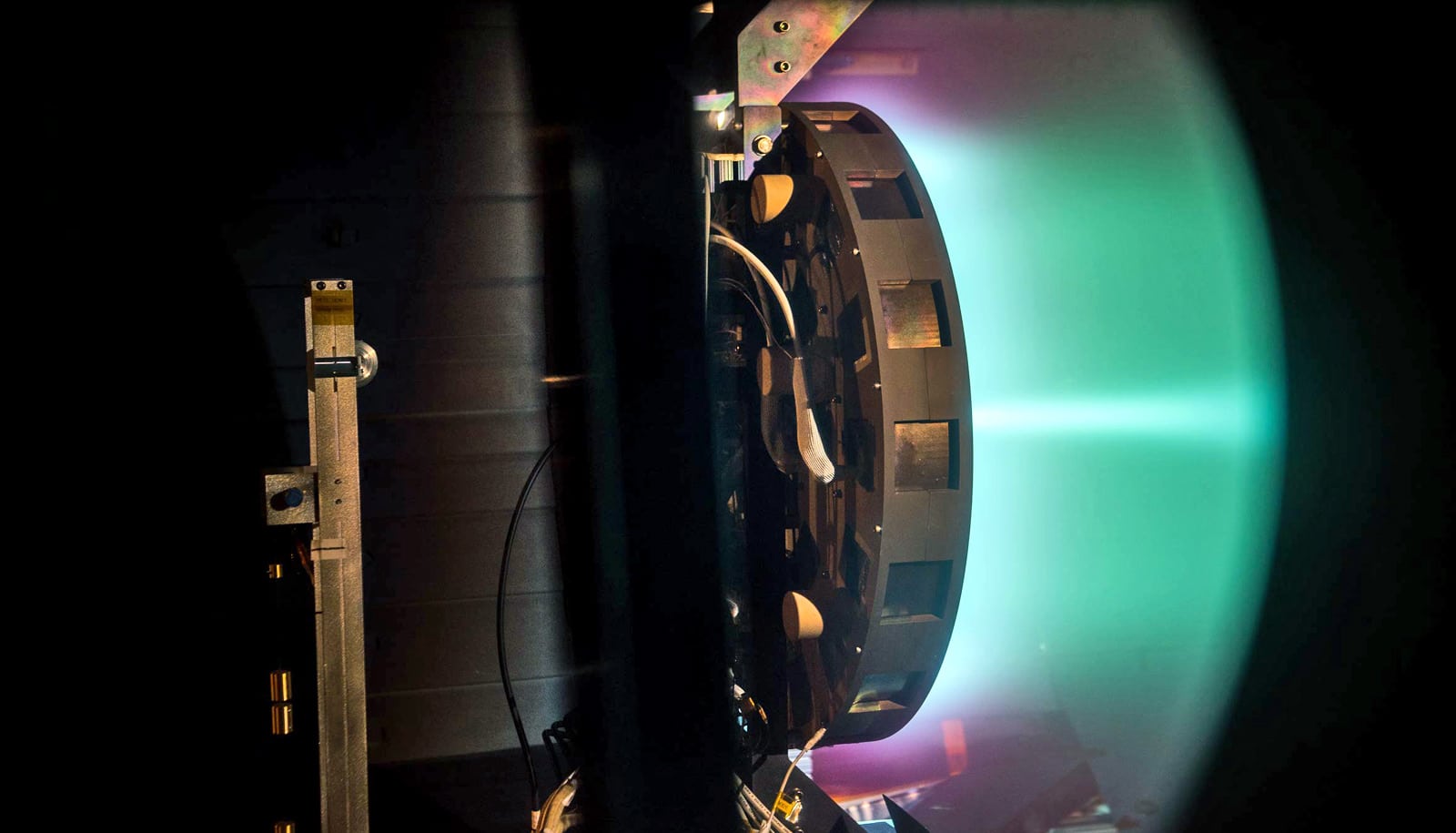
“Mars missions are just on the horizon, and we already know that Hall thrusters work well in space,” says Alec Gallimore, professor of aerospace engineering and of applied physics at the University of Michigan.
The improvement in thrust is especially important for a crewed mission—it means faster acceleration and shorter travel times.
“They can be optimized either for carrying equipment with minimal energy and propellant over the course of a year or so, or for speed—carrying the crew to Mars much more quickly.”
The challenge is to make Hall thrusters larger and more powerful. The new “X3” shattered the previous thrust record, coming in at 5.4 newtons of force compared with 3.3 newtons.
The improvement in thrust is especially important for a crewed mission—it means faster acceleration and shorter travel times. Also, the X3 more than doubled the operating current record (250 amperes vs. 112 amperes) and ran at a slightly higher power (102 kilowatts vs. 98 kilowatts).
The X3 is one of three prototype “Mars engines” to be turned into a full propulsion system with funding from NASA. Doctoral student Scott Hall carried out the tests at the NASA Glenn Research Center in Cleveland, along with NASA Glenn research scientist Hani Kamhawi. The experiments were the culmination of more than five years of building, testing, and improving the thruster.
NASA Glenn, which specializes in solar electric propulsion, is currently home to the only vacuum chamber in the US that can handle the X3 thruster—it produces so much exhaust that vacuum pumps at other chambers can’t keep up. Then, xenon that has been shot out the back of the engine can drift back into the plasma plume, muddying the results.
The X3 team snagged a test window from late July through August this year, starting with four weeks to set up the thrust stand, mount the thruster, and connect it with xenon and electrical power supplies.
Hall built a custom thrust stand to bear the X3’s 500-pound weight and withstand its force. “The big moment is when you close the door and pump down the chamber,” he says.
After the 20 hours of pumping to achieve a space-like vacuum, Hall and Kamhawi spent 12-hour days testing the X3.
Even small breakages feel like big problems when it takes days to gradually bring air back into the chamber, get in to make the repair, and pump the air back out again. Hall and Kamhawi brought the X3 up to its record-breaking power, current, and thrust over the 25 days of testing.
6 ways health would suffer on a trip to Mars
Looking ahead, the X3 will be integrated with the power supplies under development by Aerojet Rocketdyne, a rocket and missile propulsion manufacturer and lead on the propulsion system grant from NASA. In spring 2018, Hall expects to be back at NASA Glenn running a 100-hour test of the X3 with Aerojet Rocketdyne’s power processing system.
The project is funded through NASA’s Next Space Technologies for Exploration Partnership, which also supports habitat systems and in-space manufacturing.
Source: University of Michigan