A special 3D printing method has created a miniature metal version of Michelangelo’s David with pure copper.
The core component of the 3D printing process is a micropipette coupled to a cantilever; this makes it possible to monitor the force with which the point of the pipette touches the substrate.
With this assembly, the researchers can electrochemically deposit dissolved metals onto an electrically conductive substrate with a high degree of precision. Thanks to the optical force measurement that automates the process, they can build minuscule metal structures layer by layer.
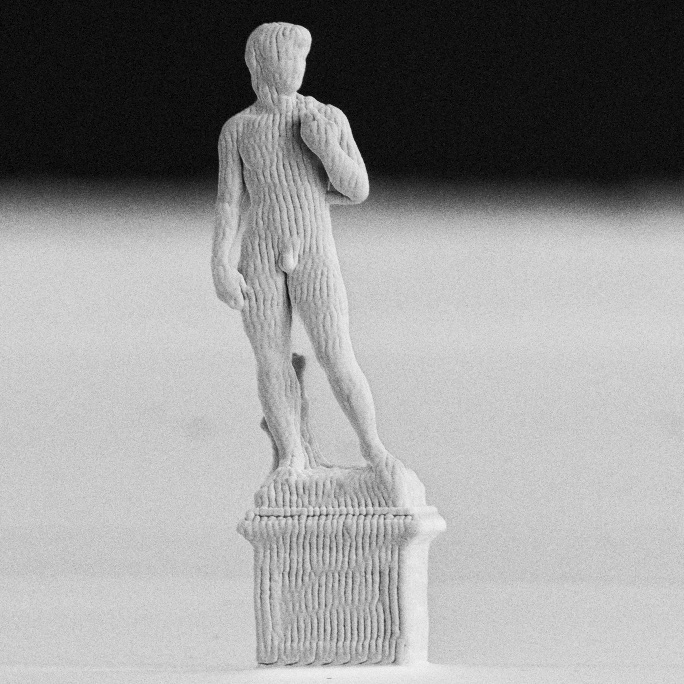
Giorgio Ercolano of Exaddon printed the micro-David to highlight the technology’s potential. Prior to that, the researchers had mostly created tiny columns or coils. “However, the process allows us to print structures or geometries of all levels of complexity,” Ercolano says. The sculpture was printed in one go, without supports or templates, and didn’t require any firing or tempering. Ercolano and colleagues report their results in the journal Micromachines.
Exaddon, an offshoot of ETH Zurich spin-off Cytosurge, worked with a team led by ETH professor Tomaso Zambelli of the Laboratory of Biosensors and Bioelectronics.
The data for the David sculpture are freely available online. “I could even have printed the room that the statue is standing in—the data includes that as well!” says Ercolano. But he chose to adjust the data set so he could reproduce Michelangelo’s David without its exhibition room.
Ercolano printed David in two sizes: first as a sculpture just 1 millimeter high, and then one 10 times smaller. “The smaller figure is only as tall as the pedestal of the larger one,” he says.
But with structures that small, achieving the required resolution becomes problematic. Printed metallic micro-objects typically start at 1 micrometer (µm), and for more complex and detailed objects, sizes range from 100 µm to 1 mm. In terms of time, too, the 1 mm model is a world away from the one that is ten times smaller: the device needed 30 hours to create the “big” David but just 20 minutes for the smaller version.
Theoretically, the system can print objects up to 5 mm in size, but the printer cartridge contains only a microliter of “ink”—just about enough for manufacturing the larger David. But it is also enough “ink” to print hundreds or even thousands of tiny objects, which represents the real strength of the process.
The printing process is of interest first and foremost to the electronics industry. With this method, manufacturers could connect computer chips together or precisely repair microelectronics systems. Although other metals can be printed, such as platinum, gold, nickel, or silver, copper is in highest demand. “Nine out of ten enquiries are about copper,” Ercolano says.
Innosuisse, the Swiss Innovation Agency, supported the work.
Source: ETH Zurich